It takes three steps to fit an elephant into a refrigerator. So how do you fit a pile of sand into a computer?
Of course, what we are referring to here is not the sand on the beach, but the raw sand used to make chips. "Mining sand to make chips" requires a complicated process.
Step 1: Obtain Raw Materials
It is necessary to select suitable sand as raw material. The main component of ordinary sand is also silicon dioxide (SiO₂), but chip manufacturing has extremely high requirements on the purity of silicon dioxide. Therefore, quartz sand with higher purity and less impurities is generally selected.
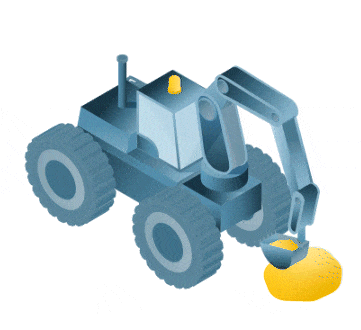
Step 2: Transformation of raw materials
To extract ultra-pure silicon from sand, the sand must be mixed with magnesium powder, heated at high temperature, and the silicon dioxide reduced to pure silicon through a chemical reduction reaction. It is then further purified through other chemical processes to obtain electronic-grade silicon with a purity of up to 99.9999999%.
Next, the electronic-grade silicon needs to be made into single crystal silicon to ensure the integrity of the processor's crystal structure. This is done by heating high-purity silicon to a molten state, inserting a seed crystal, and then slowly rotating and pulling it to form a cylindrical single crystal silicon ingot.
Finally, the single crystal silicon ingot is cut into extremely thin wafers using a diamond wire saw and the wafers are polished to ensure a smooth and flawless surface.
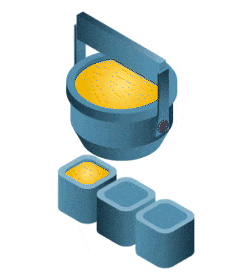
Step 3: Manufacturing Process
Silicon is a key component of computer processors. Technicians use high-tech equipment such as photolithography machines to repeatedly perform photolithography and etching steps to form layers of circuits and devices on silicon wafers, just like "building a house." Each silicon wafer can accommodate hundreds or even thousands of chips.
The fab then sends the finished wafers to a pre-processing plant, where a diamond saw cuts the silicon wafers into thousands of individual rectangles the size of a fingernail, each of which is a chip. Then, a sorting machine selects qualified chips, and finally another machine puts them on a reel and sends them to a packaging and testing plant.
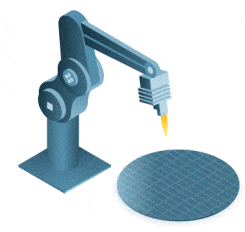
Step 4: Final Packaging
At the packaging and testing facility, technicians perform final tests on each chip to ensure that they are performing well and are ready for use. If the chips pass the test, they are mounted between a heat sink and a substrate to form a complete package. This is like putting a "protective suit" on the chip; the external package protects the chip from damage, overheating, and contamination. Inside the computer, this package creates an electrical connection between the chip and the circuit board.
Just like that, all kinds of chip products that drive the technological world are completed!
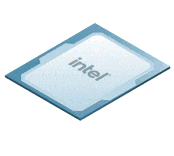
INTEL AND MANUFACTURING
Today, the transformation of raw materials into more useful or valuable items through manufacturing is an important driver of the global economy. Producing more goods with less material or fewer man-hours and improving workflow efficiency can further increase product value. As companies produce more products at a faster rate, profits throughout the business chain increase.
Manufacturing is at the core of Intel.
Intel makes semiconductor chips, graphics chips, motherboard chipsets, and other computing devices. As semiconductor manufacturing becomes more complex, Intel is one of the few companies in the world that can complete both cutting-edge design and manufacturing in-house.
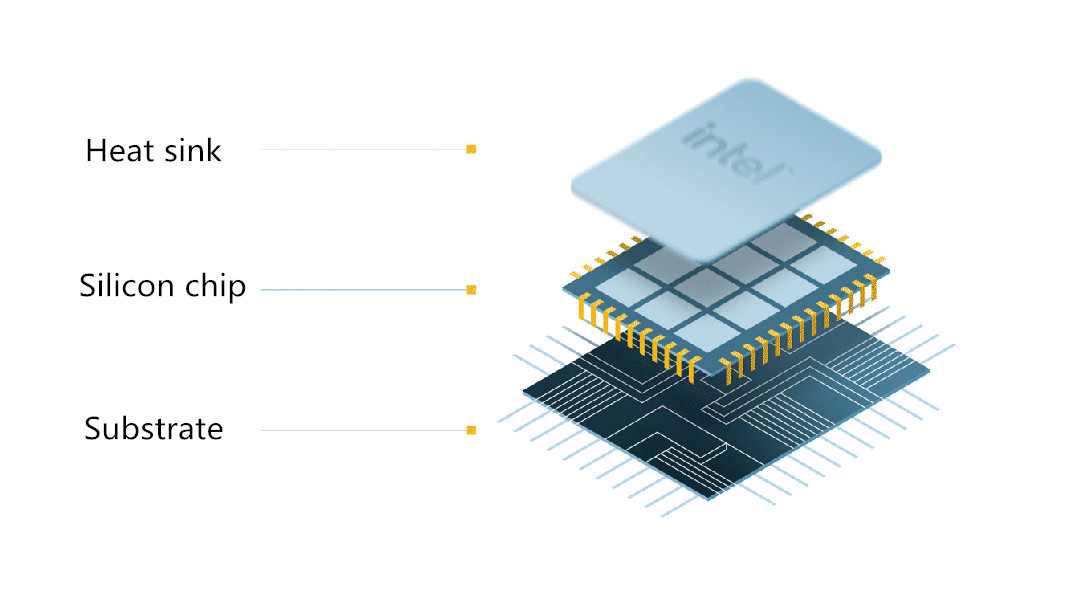
Since 1968, Intel engineers and scientists have overcome the physical challenges of packing more and more transistors into smaller and smaller chips. Achieving this goal requires a large global team, leading-edge factory infrastructure, and a strong supply chain ecosystem.
Intel's semiconductor manufacturing technology evolves every few years. As predicted by Moore's Law, each generation of products brings more features and higher performance, improves energy efficiency, and reduces the cost of a single transistor. Intel has multiple wafer manufacturing and packaging test facilities around the world, which operate in a highly flexible global network.
MANUFACTURING AND DAILY LIFE
Manufacturing is essential to our daily lives. The items we touch, rely on, enjoy and consume every day require manufacturing.
Simply put, without transforming raw materials into more complex items, there would be no electronics, appliances, vehicles, and other products that make life more efficient, safer, and more convenient.
Post time: Feb-03-2025