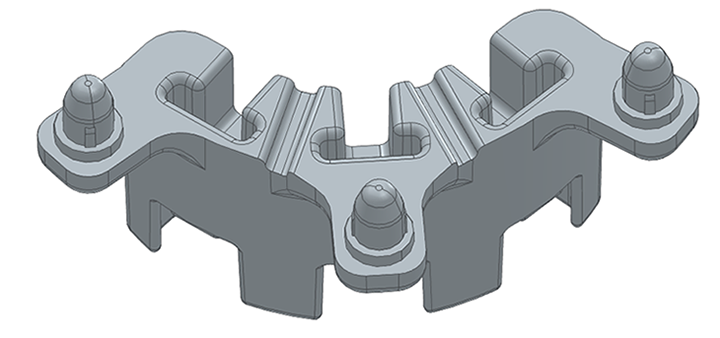
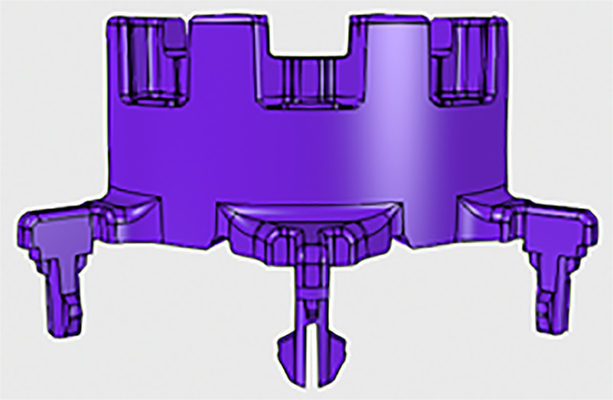
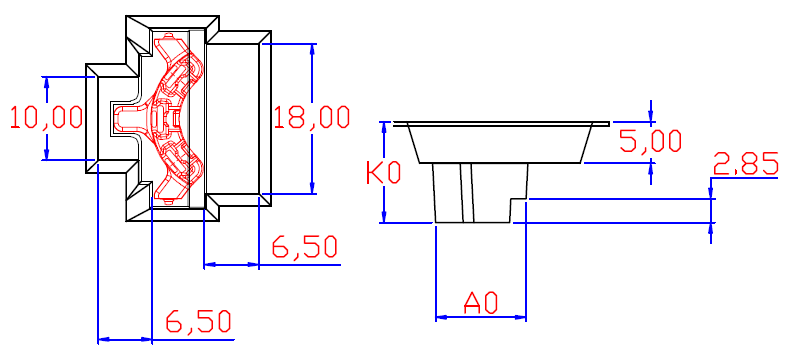
Injection molding is a highly efficient manufacturing process widely used in the automotive industry to produce a variety of components. This technique involves injecting molten material, typically plastic, into a mold to create parts with precise dimensions and complex geometries.
Problem:
In May 2024, one of our customers, a Manufacturing Engineer from an automotive company, requested that we provide a custom carrier tape for their injection-molded parts. The part requested is called a "hall carrier.” It is made of PBT plastic and has dimensions of 0.87” x 0.43” x 0.43”, with a weight of 0.0009 lbs. The customer specified that the parts should be oriented in the tape with the clips facing downward, as illustrated below.
Solution:
To ensure enough clearance for the robot's grippers, we will need to design the tape to accommodate the required space. The necessary clearance specifications for the grippers are as follows: the right claw requires a space of approximately 18.0 x 6.5 x 4.0 mm³, while the left claw needs a space of about 10.0 x 6.5 x 4.0 mm³. Following all of the above discussions, Sinho's engineering team designed the tape in 2 hours and submitted it for customer approval. We then proceeded to process the tooling and create a sample reel within 3 days.
One month later, the customer provided feedback indicating that the carrier worked exceptionally well and approved it. They have now requested that we provide a PPAP document for the verification process for this ongoing project.
This is an excellent custom solution from Sinho's engineering team. In 2024, Sinho created over 5,300 custom carrier tape solutions for various components for different electronic components manufacturers in this industry. If there is anything we can assist you with, we are always here to help.
Post time: Oct-15-2024